Stucco decoration
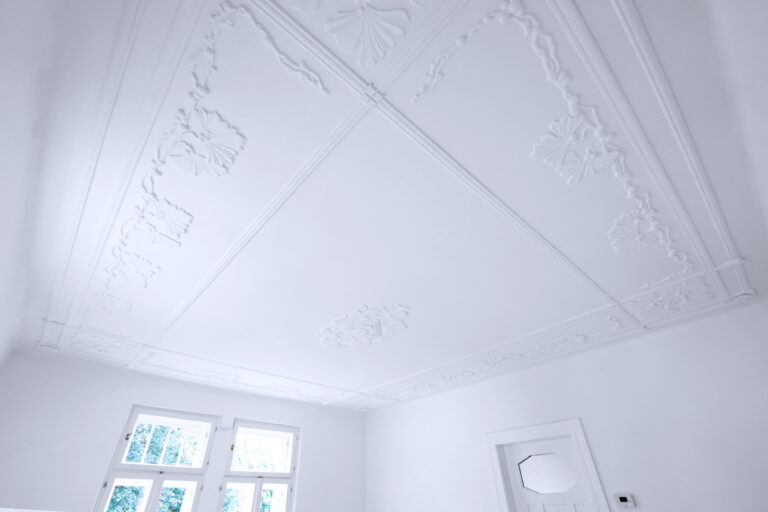
Our goal is to improve the quality of the spaces and to highlight their strengths. With a passion for architecture and modern technology, we have created a process that combines architecture with production automation through 3D printing, virtual models and precision execution. After thoroughly developing workflows and testing materials, we proceeded to implement the first projects, which are constantly being refined.
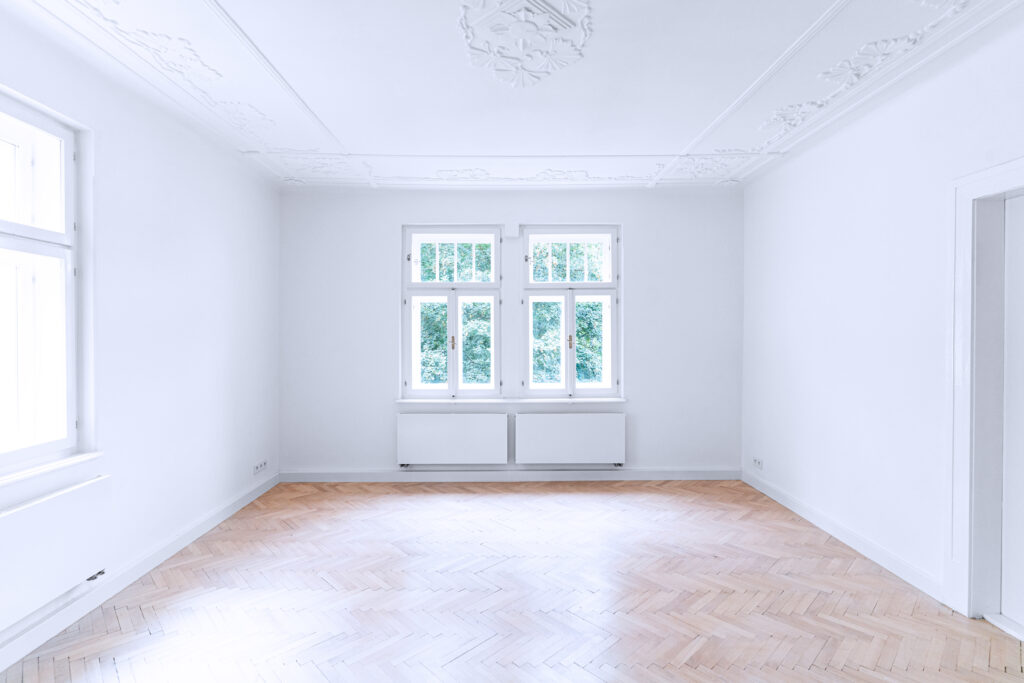
Concept
We use repeatable motifs for easy implementation. Each space has its own unique plan, composed of a limited number of replicated parts that are seamlessly connected to each other. Through thoughtful design, we create organic motifs without noticeable repeating assemblies, which simplifies implementation and ensures aesthetic quality. The installation is based on 1:1 scale plans, where the individual parts are precisely positioned and connected to form a unified whole.
Proposal
Our service begins with the development of a proposal in collaboration with the client. Together we determine the expectations and concept of the decoration. We like to work with the hierarchy of each room and reflect their purpose and intimacy in the design. We tailor the complexity and ornateness of the installation accordingly.
The process continues with the creation of a detailed plan that outlines the spatial layout of the installation. The first step is to accurately measure the areas on which the installation will be implemented. The plan is composed of individual elements that symbolize the production parts. We can work with precise, geometric elements as well as free-flowing, organic parts of the design during design and implementation.
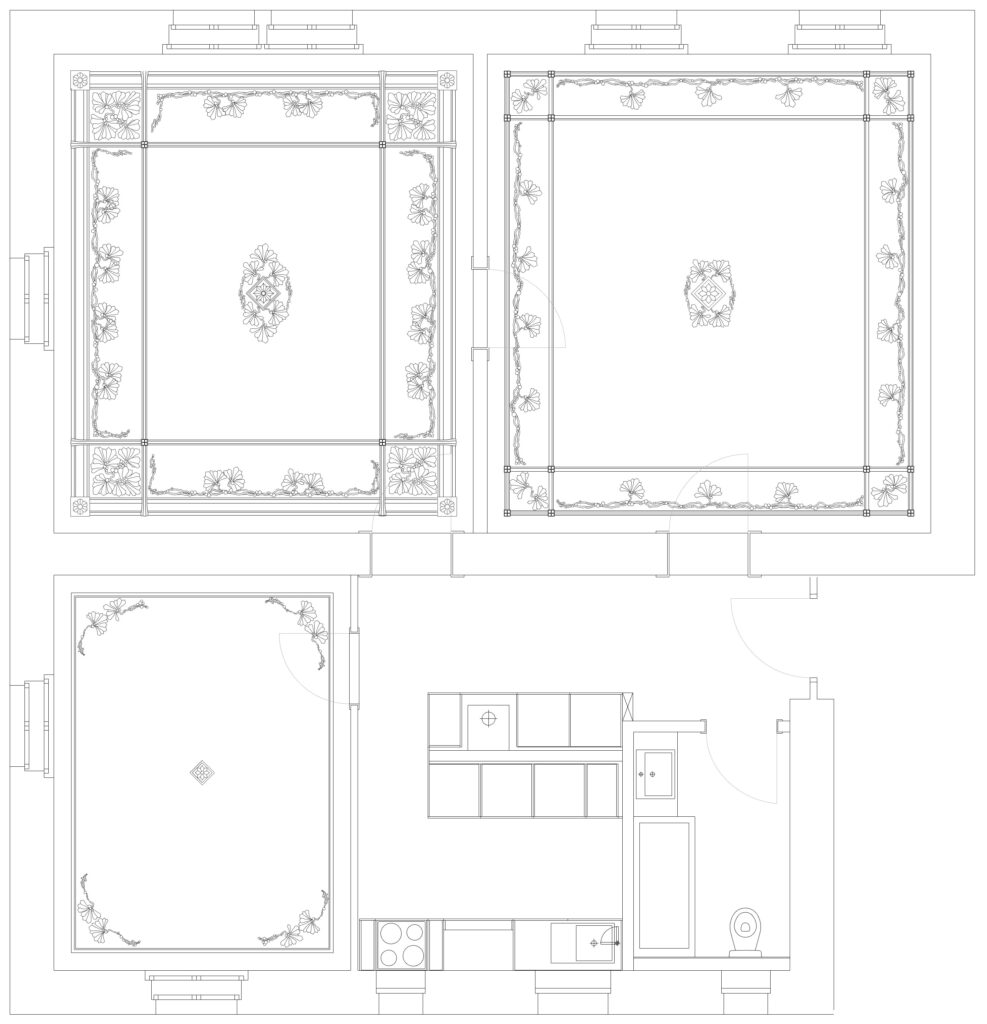
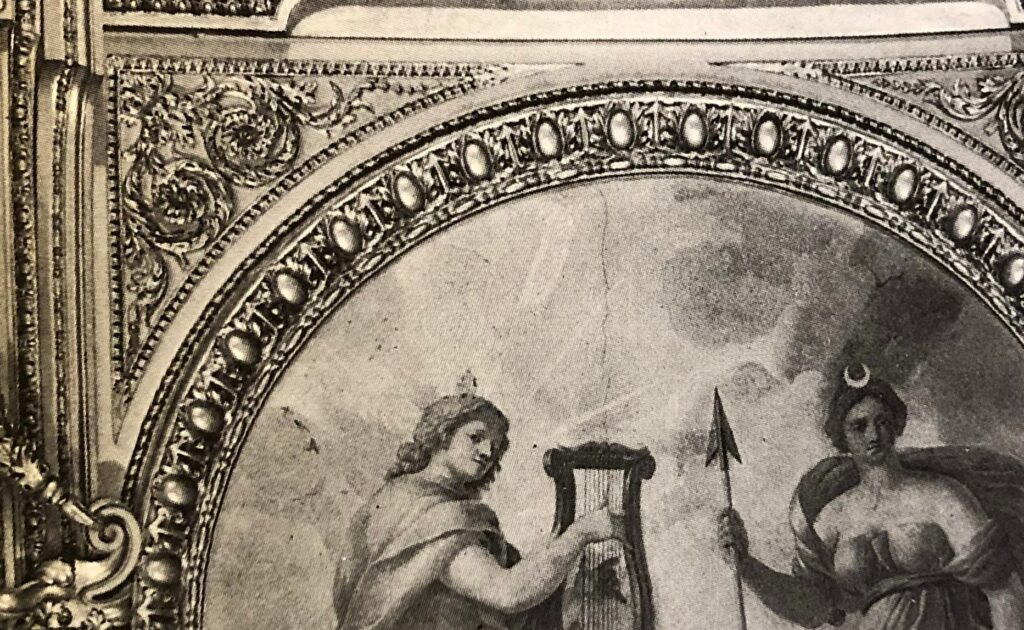
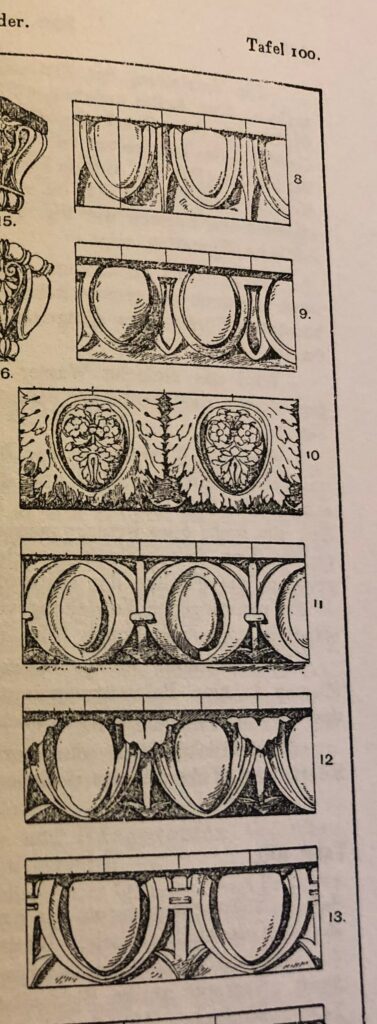
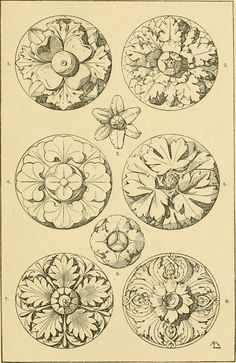
Implementation
The first step of implementation is the preparation of digital documents. Each element is modelled in detail in 3D. The key is to create precise profiles on the edges of the elements to ensure that the individual parts flow seamlessly and provide smooth transitions. After the basic model is created, each element is fitted with a reinforcing backing. Installation holes for screws are added at suitable and easily repairable locations. Each part is checked against the maximum print area of the 3D printer and split if necessary, ensuring that the joints are easily machined afterwards. Finally, parts are labeled for better organization of molds and finished products.
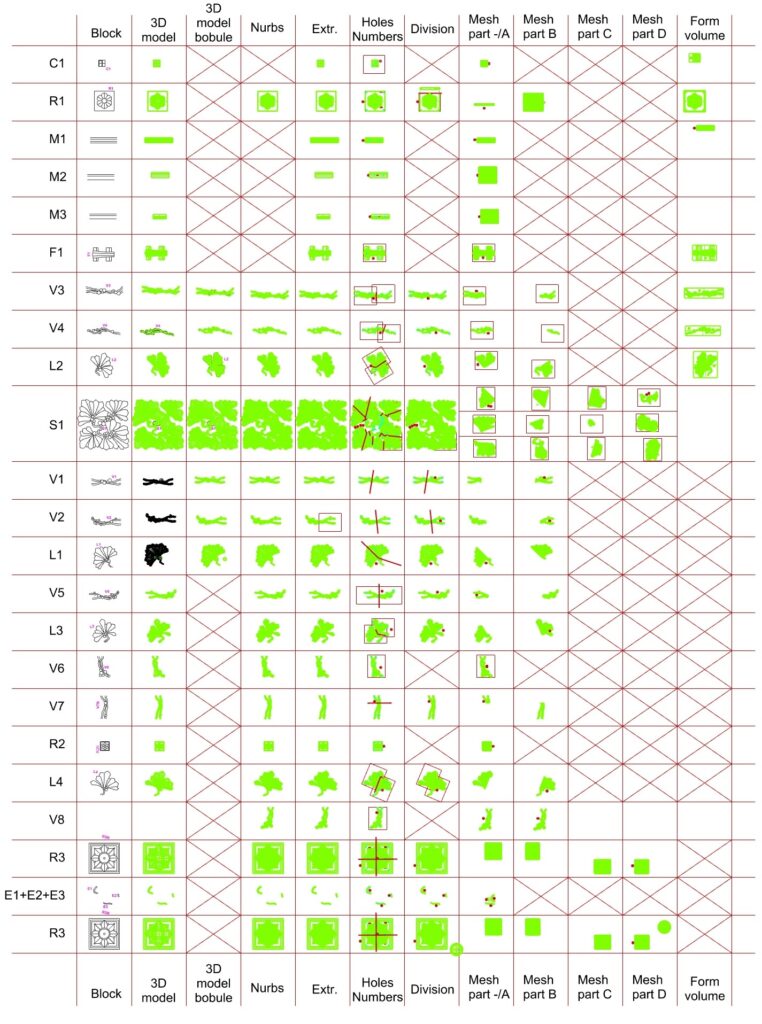
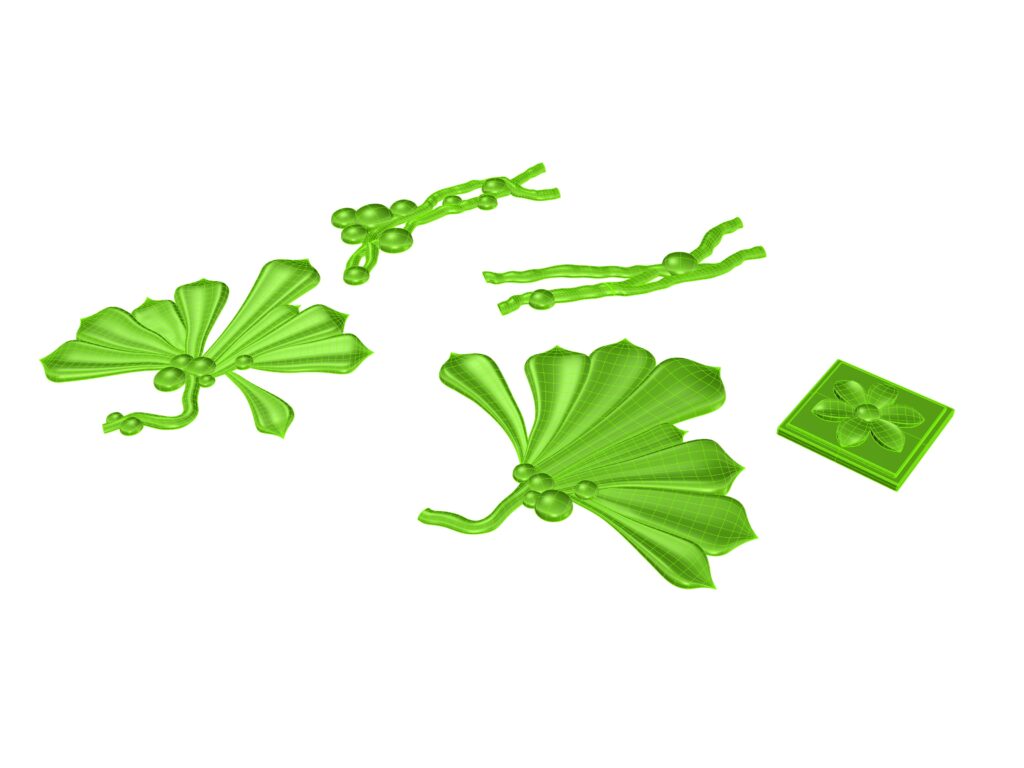
Each part is converted into a detailed mesh model and exported in .stl format. This model is then converted to G-code using slicing software, which serves as the input format for the 3D printer.
The parts are printed on the FFM 3D printer. Based on the prototype development, PET-G was chosen as the most suitable material due to its mechanical resistance, higher melting temperature and smoother print surface, which is essential for the next steps.
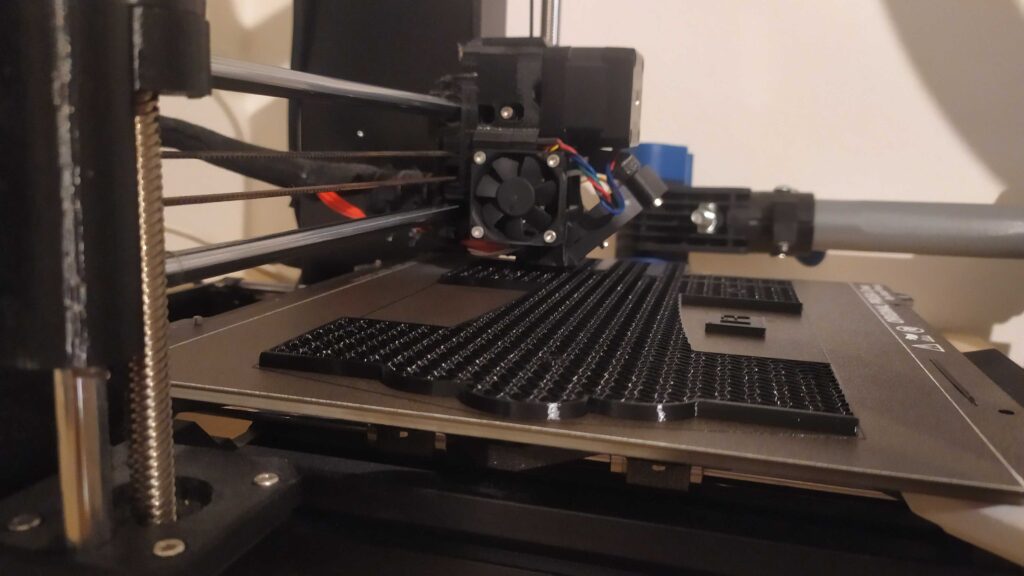
The prints from the 3D printer serve as hooves – the foundations for the production of casting moulds. Each print is thoroughly machined before further use. During inspection, we remove overprints, hems, burrs or filaments. Minor imperfections are removed with hot air, and the surface is sanded at the end to soften and reduce the visibility of the print layers.
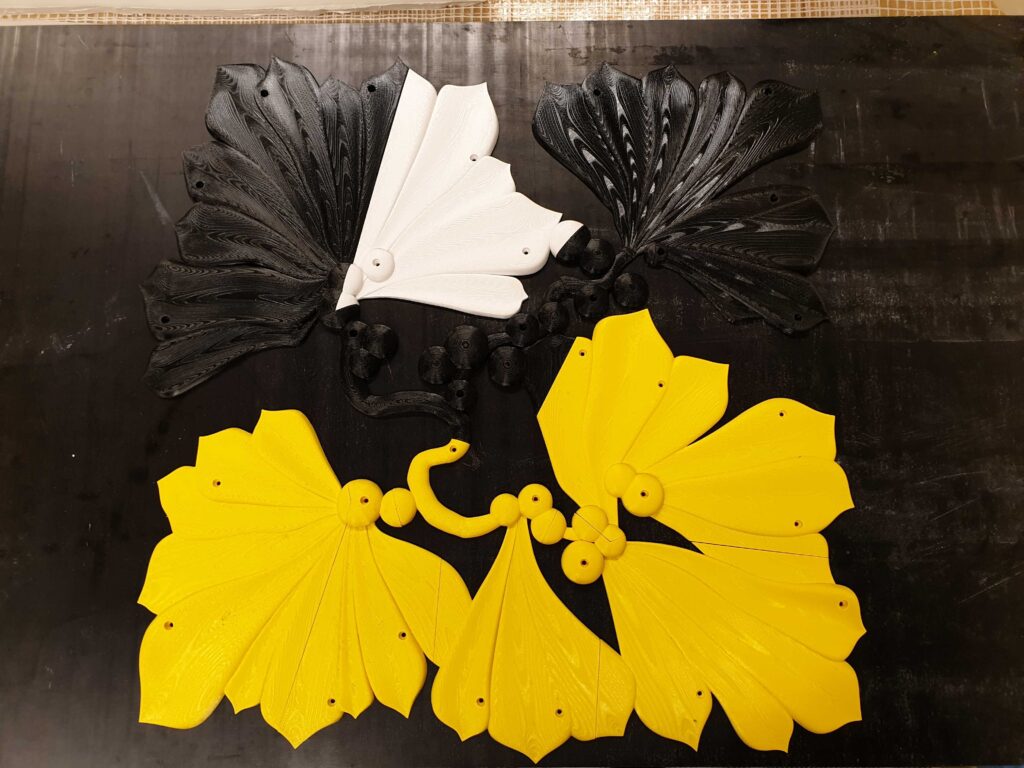
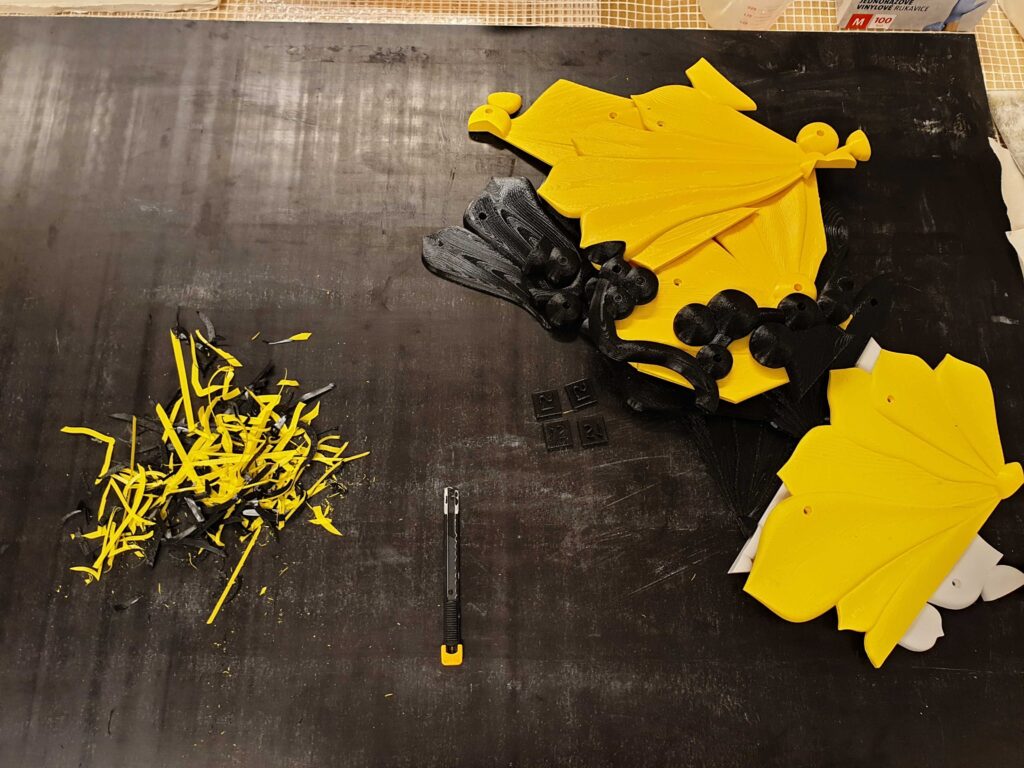
Each print is adhered to a flat backing with a smooth surface. The individual parts of the elements are precisely aligned. If necessary, sand the mating surfaces and seal the joints, including the joint between the part and the backing.
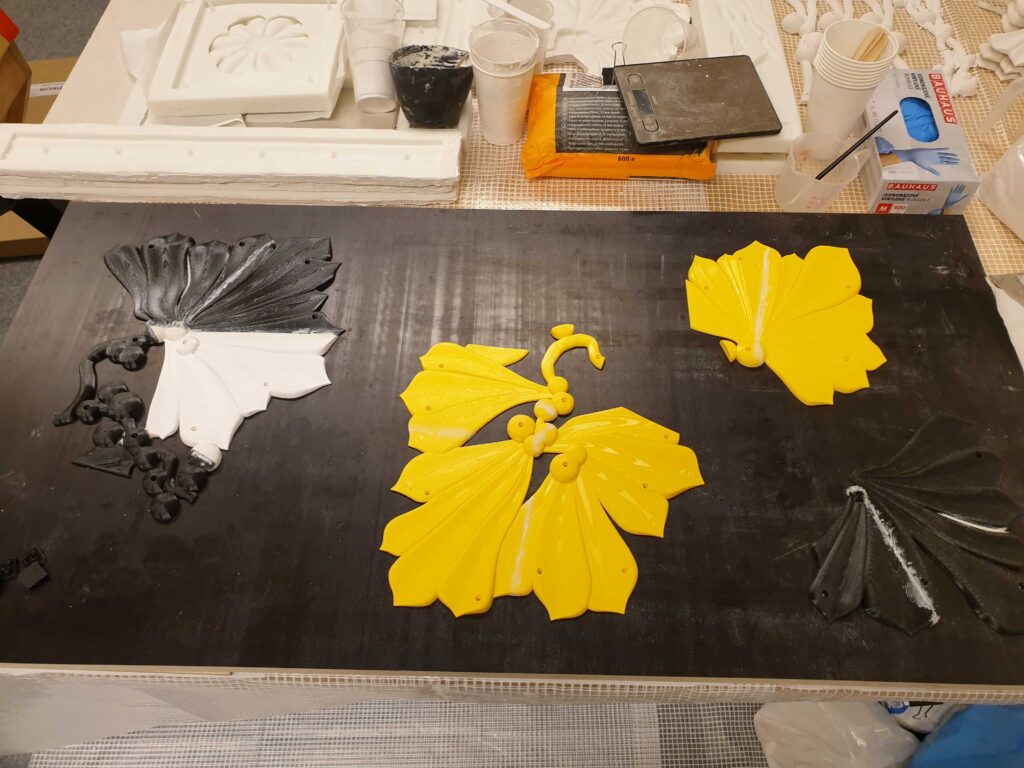
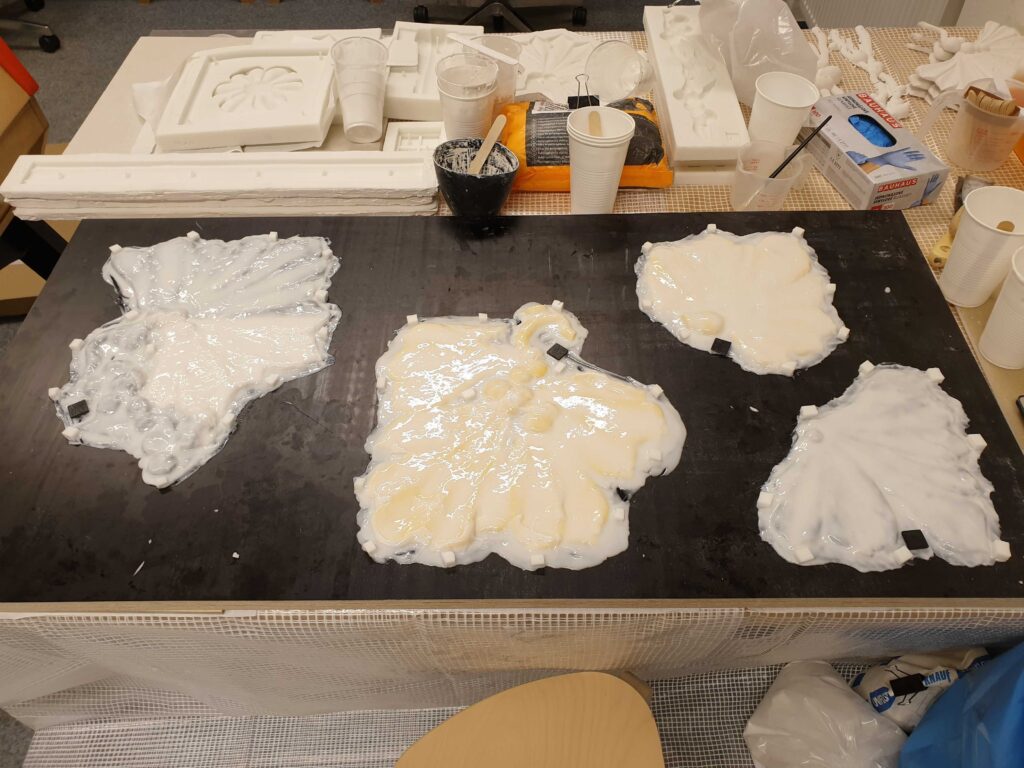
On the basis of the prepared hoof, a casting mould consisting of two parts is created. The first is a silicone layer that is applied directly to the hoof and follows its exact shape. After the silicone has cured, a second layer of plaster is added – the cadlub. This layer gives the silicone support and prevents deformation. It also reduces the consumption of silicone by using a cheaper material.
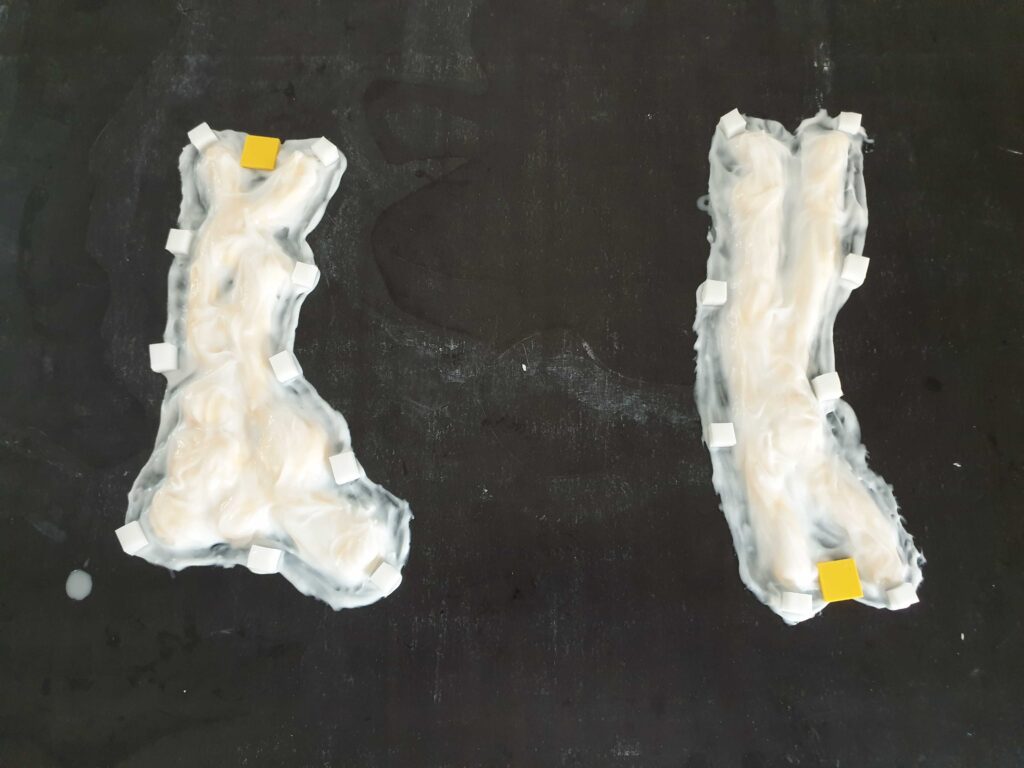
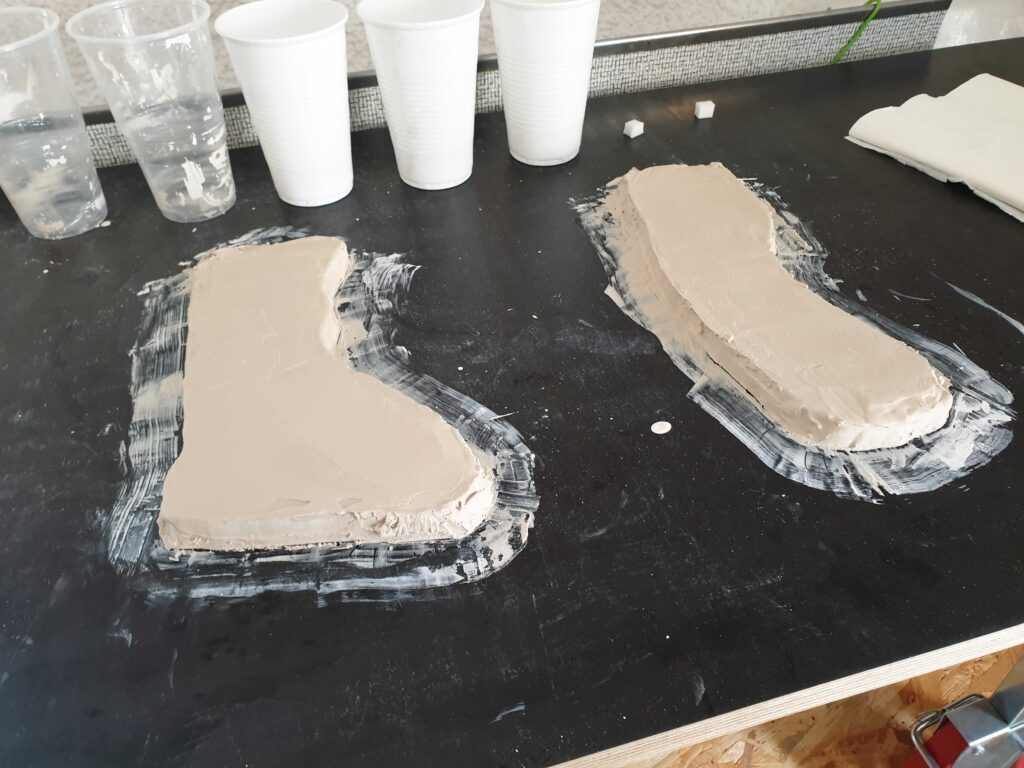
Then we proceed to the casting of the individual parts. We have developed a proprietary material that ensures sufficient strength and durability of the products, which facilitates handling and extends the life of the installation. The parts are cast in the moulds created in the required number according to the design. Each part and mould is embossed with a mark for easy identification. After partial curing, the parts are removed from the moulds.
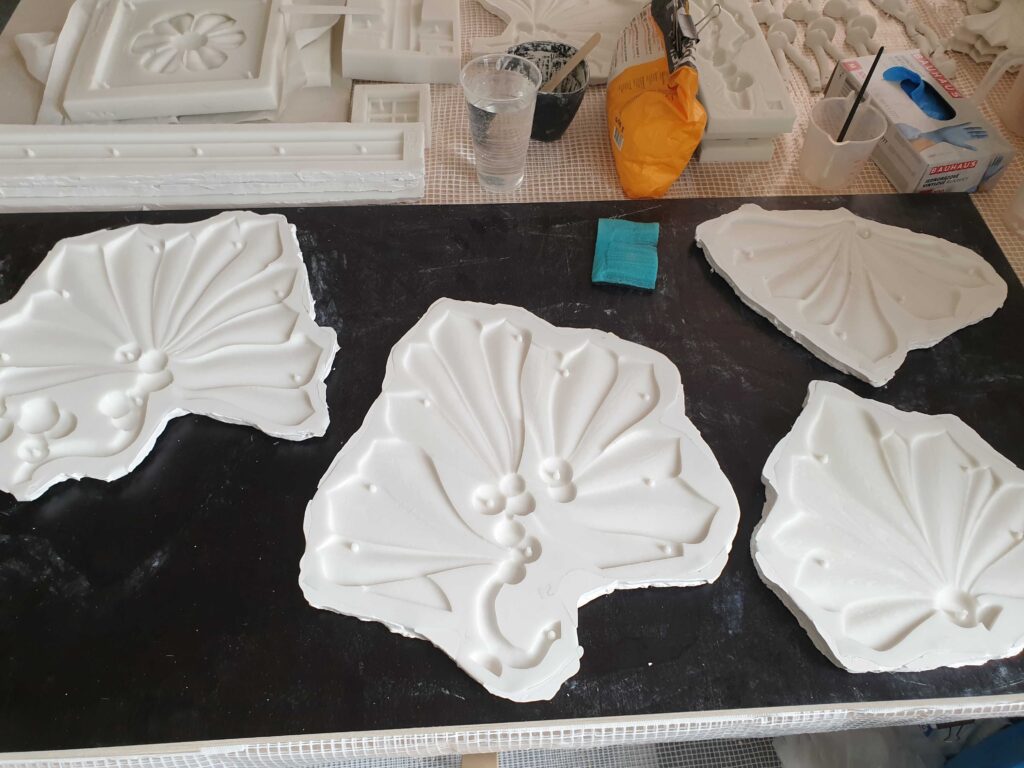
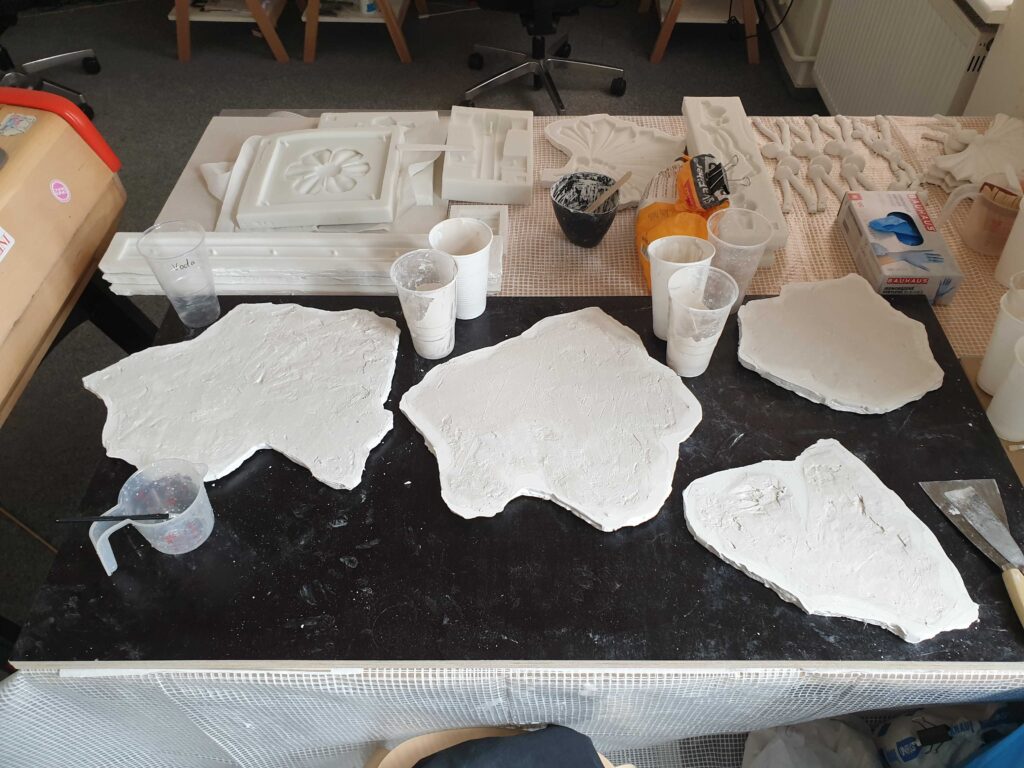
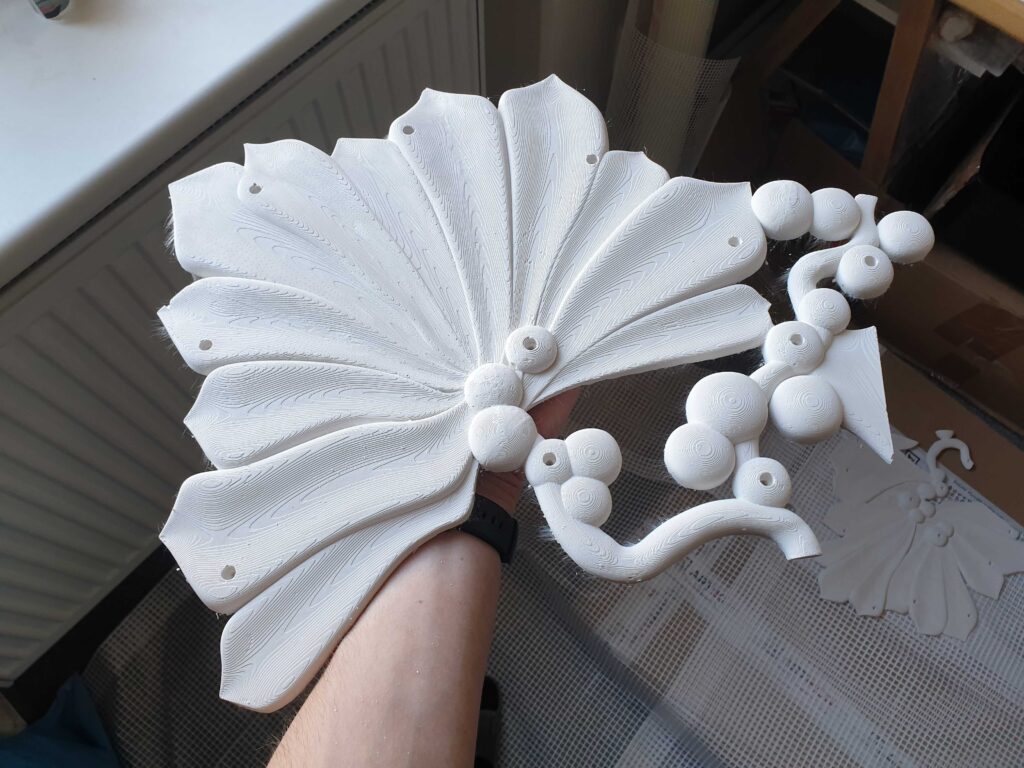
We then move to the installation site. The 1:1 scale plan is transferred to the ceiling, where the basic points and lines defining the installation position are marked. Using a projector aligned to the measured points, we mark the positions of the individual elements and their names on the ceiling.
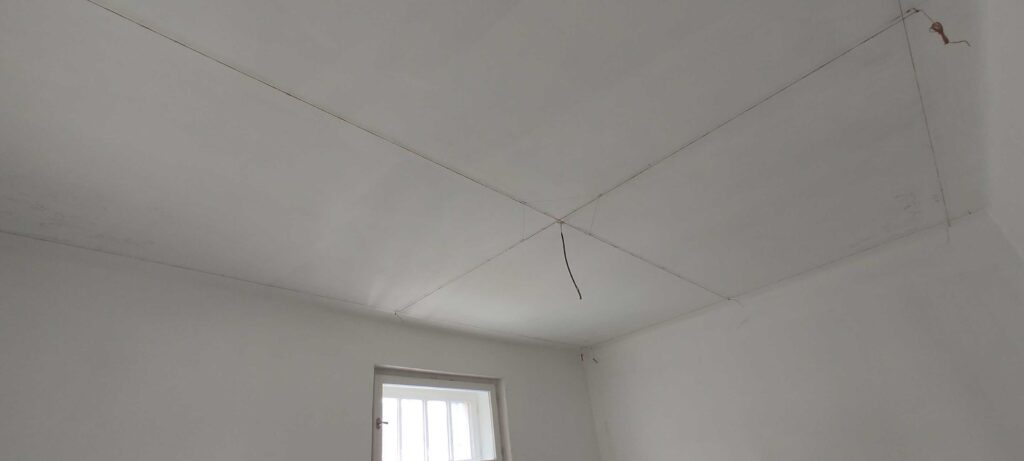
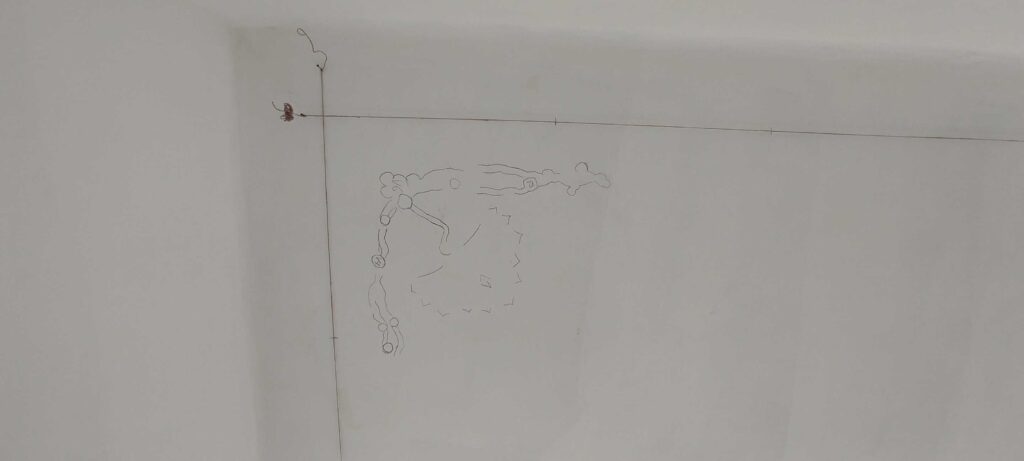
The parts are installed and anchored in two steps: using screws in the ceiling and adhesive sealant to ensure adhesion to the surface and also to fill the gaps between the casting and the uneven ceiling.
Once all the parts have been installed, the whole assembly is retouched. The joints between the parts and the installation holes for the screws are sealed, the surface sanded and any inaccuracies removed. If any imperfections are still visible, this procedure is repeated.
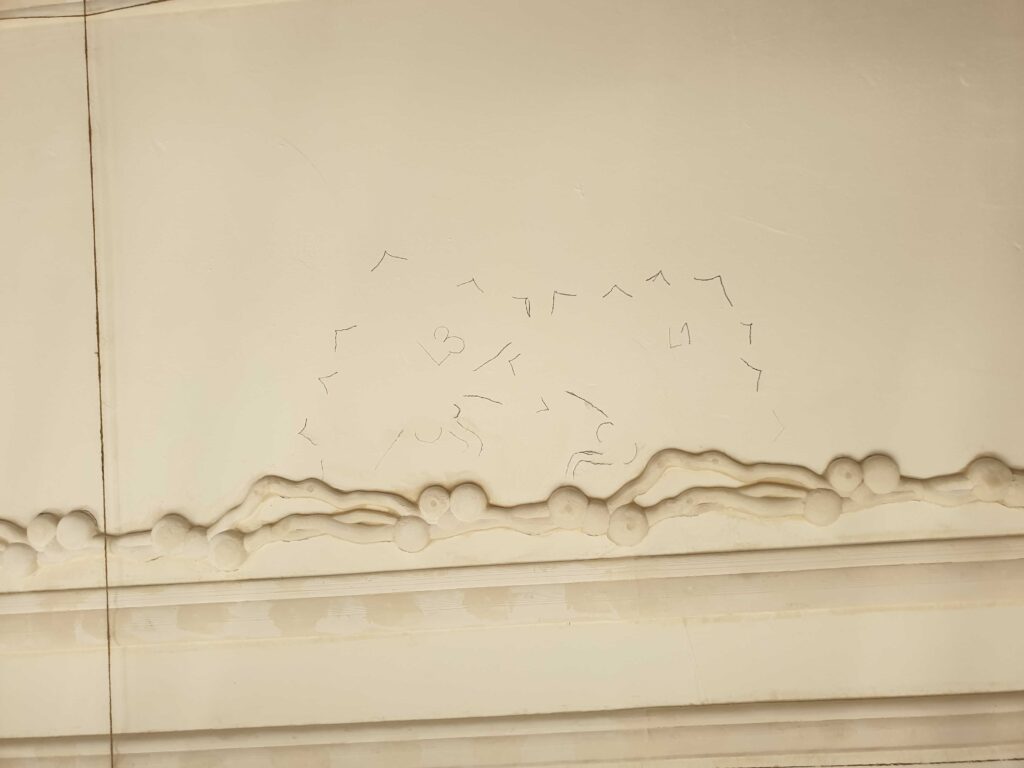
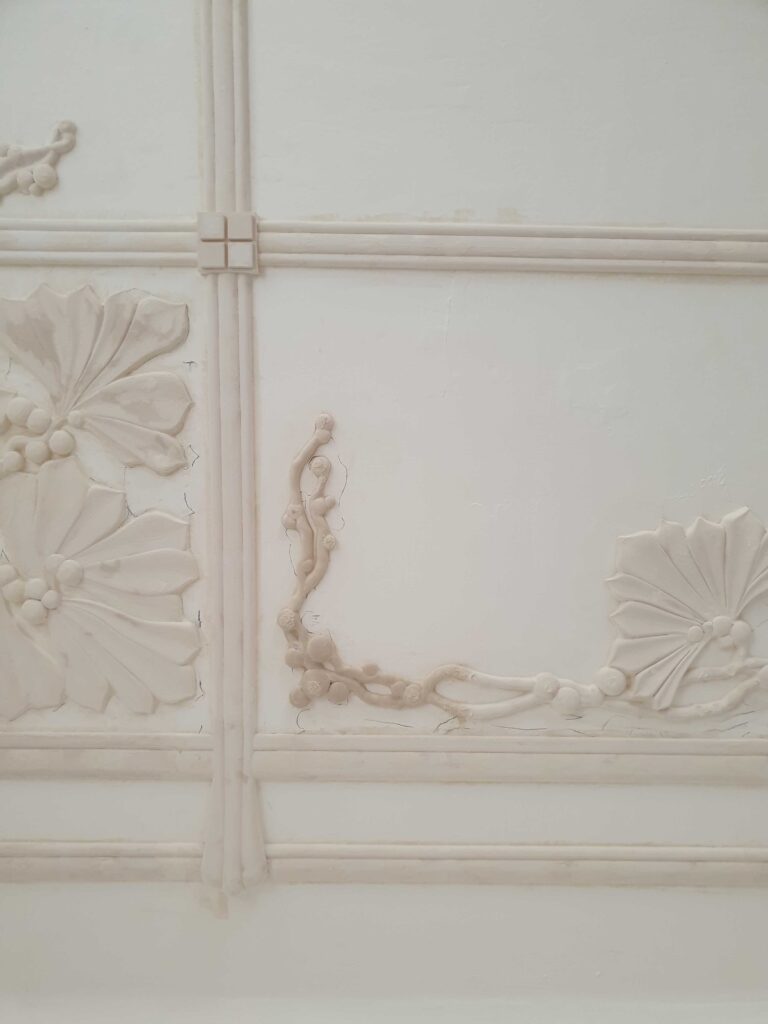
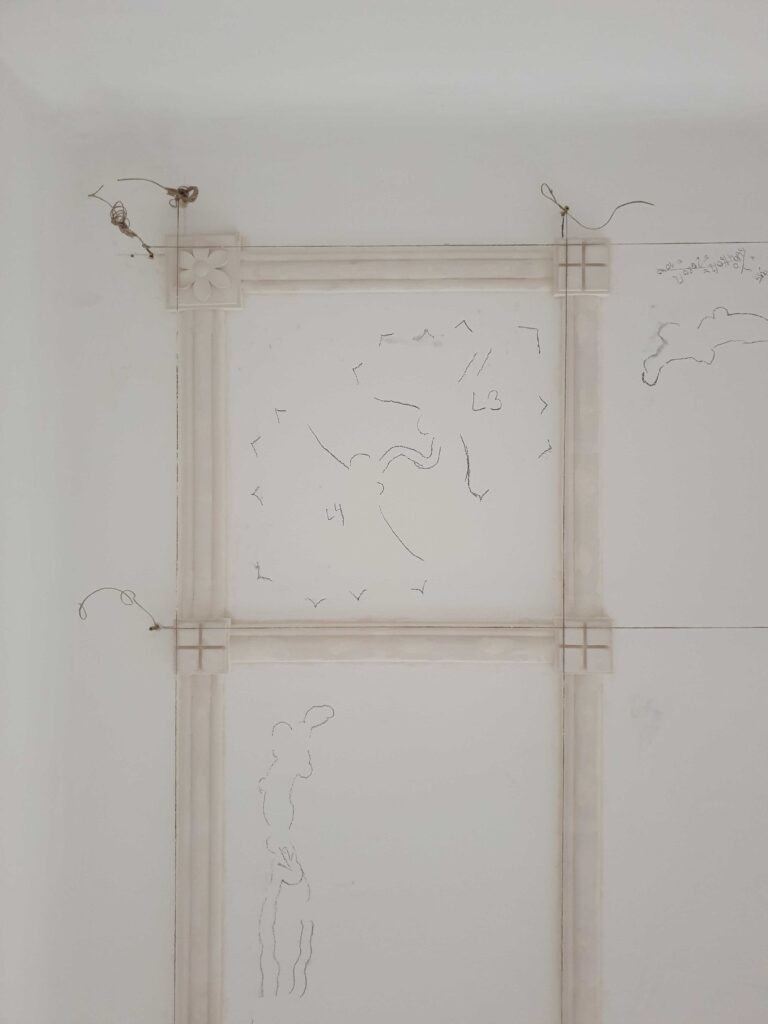
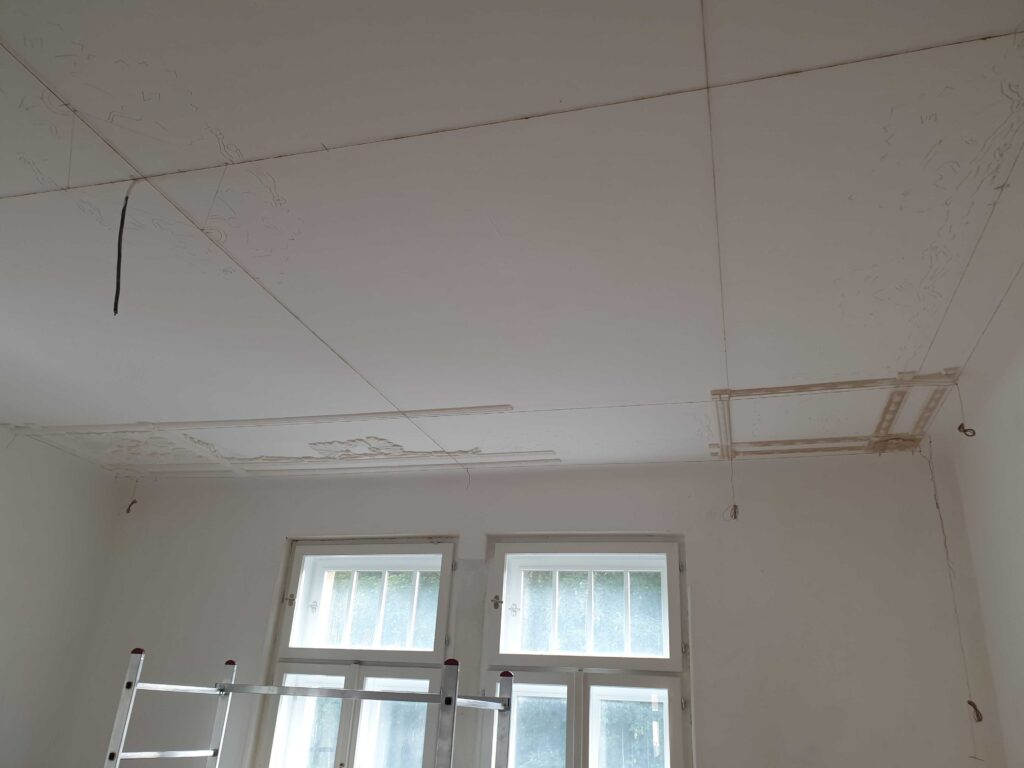
The final surface of the installation is coated with paint, which is applied with spray guns to achieve a uniform appearance. The paint is also applied to the surrounding areas to ensure that the entire surface is perfectly unified.
If the final coat reveals further imperfections, additional sealing and reapplying of paint to the problem areas is carried out.
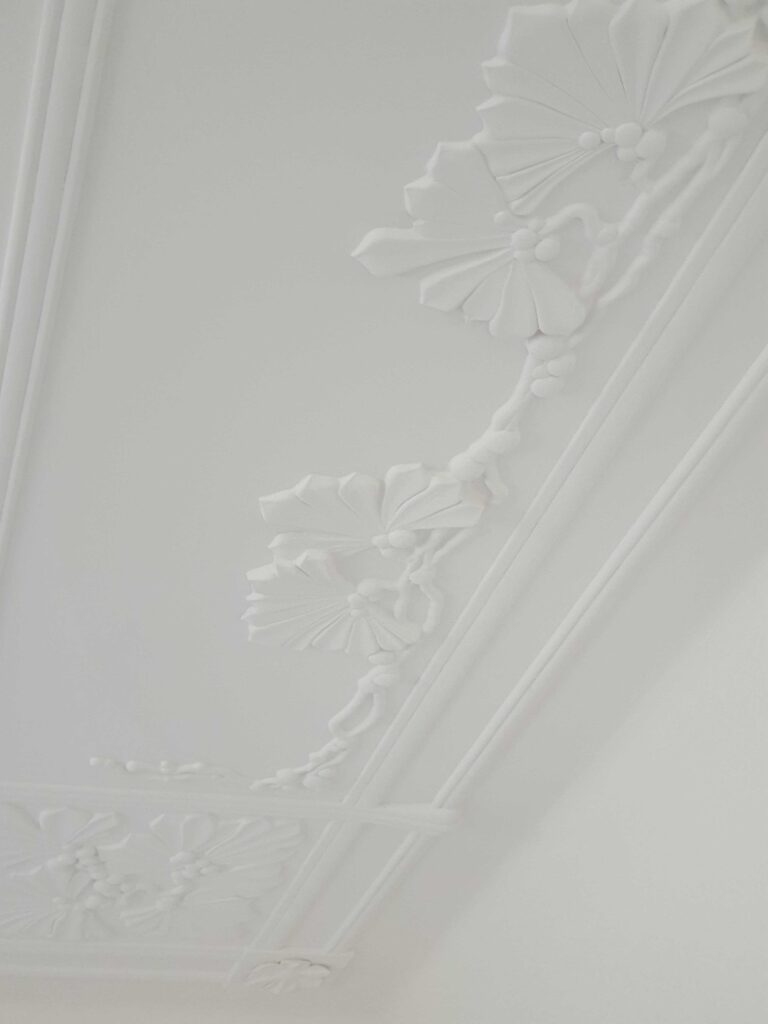
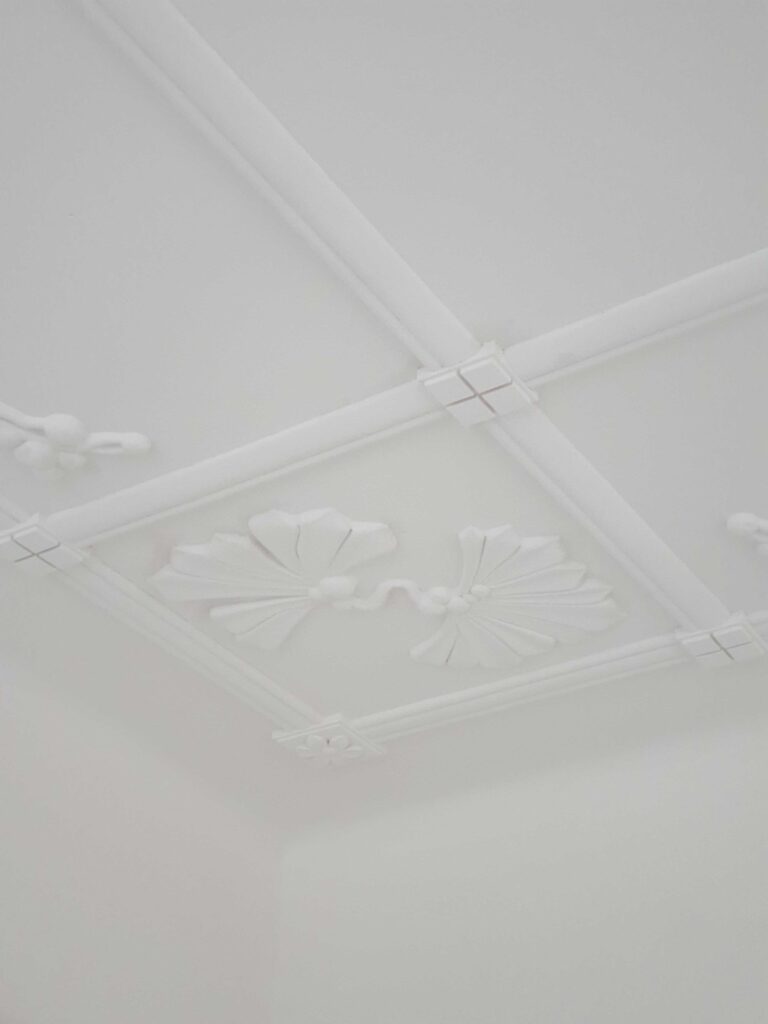
Klíčové vlastnosti
- Customized design: A unique solution for any space.
- Repeatability: Sophisticated parts allow easy replication without repeating patterns.
- Simplicity: Part of the production is prefabricated, which makes the production process and installation time more efficient.
Result
The resulting installation combines precise design, modern technology and quality craftsmanship. The production tools and moulds allow for repeatability, so that we can realise the decoration even on large areas.
In addition to the result itself, a set of production tools is also created. Thanks to the quality workmanship and durability of the moulds and plastic models, we can repeat the process at any time.
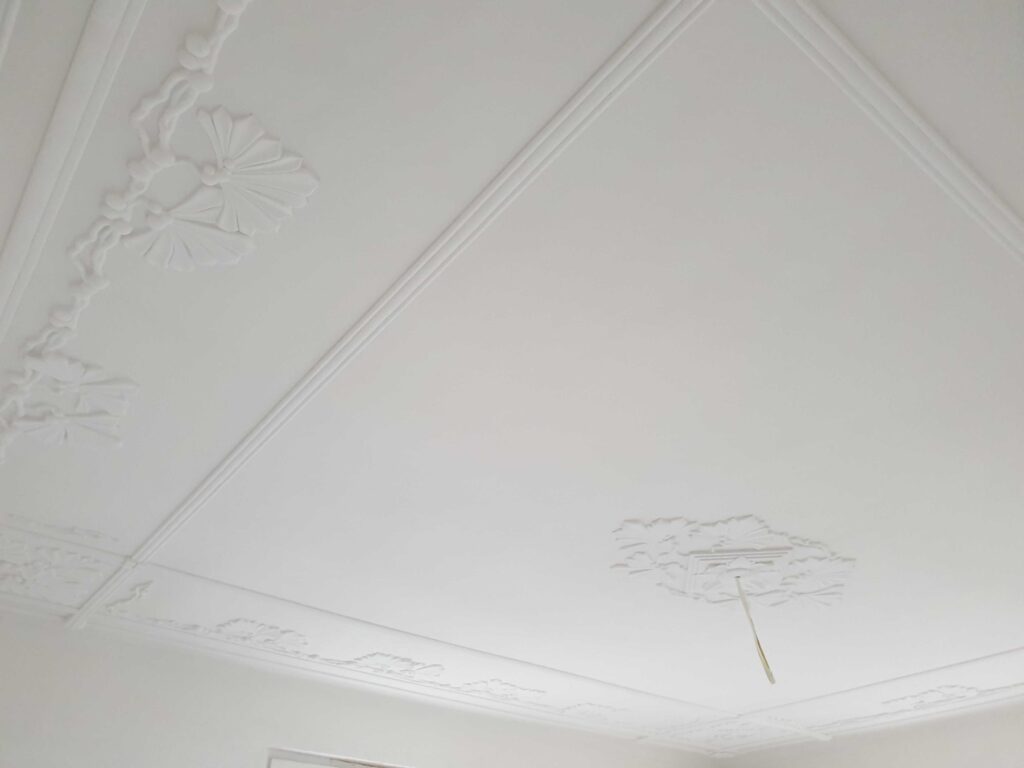
Summary
This process combines close collaboration with the client, detailed planning and advanced digital technology. From the beginning, we work closely with the client to ensure the best possible implementation of their vision. We offer efficient workflows and a creative approach to solutions using modern technology. As a result, we help to enhance and accentuate the designed spaces through non-typical installation, thus achieving added value to the interior.
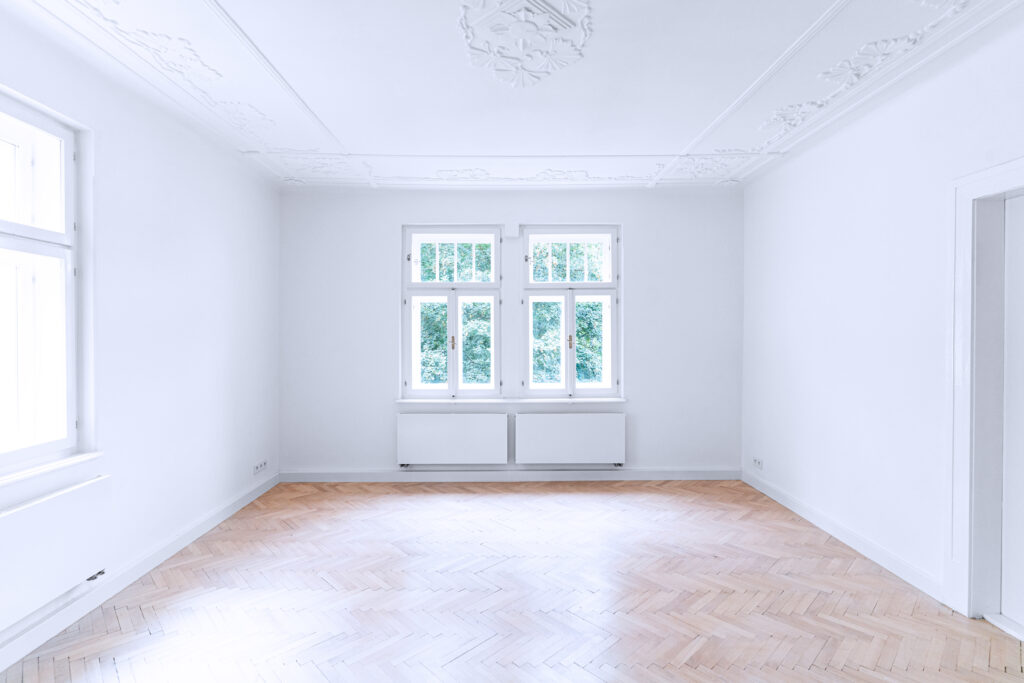
See more information and the full video of the process on our partner ioLabs’ channels: